Data & Certifications
GTO Aluminum: Your Trusted Quality Source
GTO Data & Certifications
Our products have passed Dade County testing for TAS201, TAS202, and TAS203, and are fully approved from Dade county. Our products feature 6063-T5 aluminum, non-combustible, Class A fire rating, and electrostatic powder coating.
Quality Certification Compliance
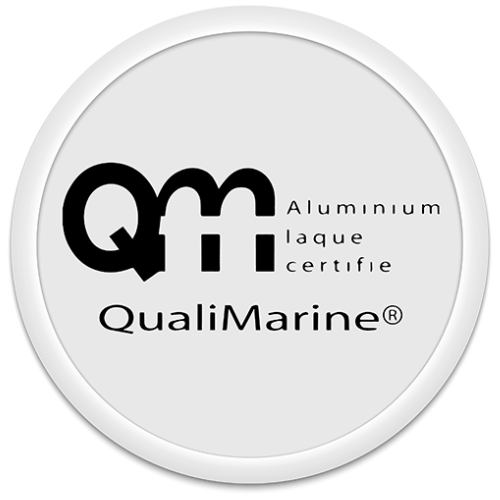
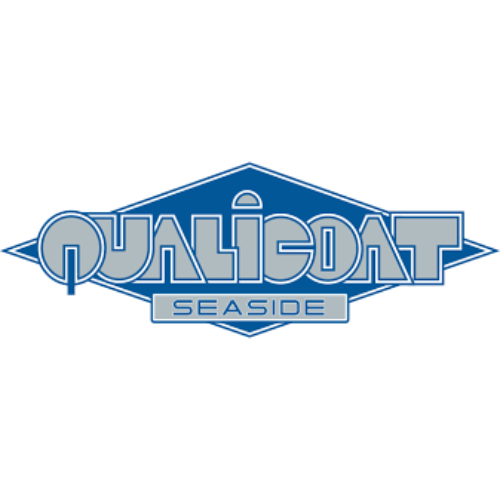
Qualimarine & Seaside Class Certifications
The Qualimarine and Seaside Class certifications, both offered by Qualicoat, are related to the durability of powder coatings in marine or coastal environments, but they have distinct standards and geographical implications.
Qualimarine is a quality label designed specifically for aluminum profiles and accessories used in marine and coastal environments. It requires rigorous testing of powder coatings to ensure their ability to withstand harsh conditions without significant deterioration.
In contrast, the Seaside Class, introduced by Qualicoat in 2008, emphasizes the pre-treatment of aluminum extrusions before powder coating. This involves a more intensive preparation process, including deeper acid or a combination of acid and alkaline etching, reaching a depth of 2 g/m2 (in comparison to the standard 1 g/m2). This is followed by a conversion layer that seals the aluminum surface, providing enhanced protection against corrosion. Notably, the Seaside Class exceeds the standards set by the British Standard and European Norm 12206-1:2004, and is suitable for aluminum used within 5 kilometers of coastal or tidal estuaries.
The primary distinction between the two lies in the pre-treatment process. The Seaside Class mandates a more thorough etching, offering superior substrate protection and improved adhesion for the powder coating. This level of treatment is essential in environments with high exposure to corrosive elements.
Products with Qualimarine & Seaside Class Certifications are available as paid upgrade.
Sustainability Information
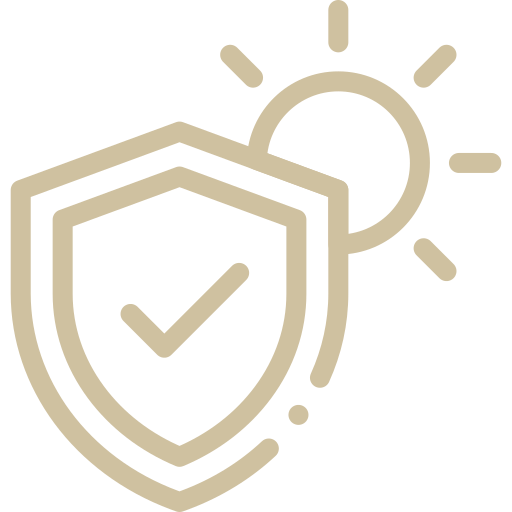
UV Exposure and QUV Testing
Our products have undergone and passed rigorous testing in a solar box for 2,000 to 4,000 hours, which is equivalent to 20 years in regular weather conditions. This testing process, involving UV exposure and QUV testing, is essential to determine the durability of a powder coating when exposed to ultraviolet (UV) light. UV radiation, particularly from sunlight, can gradually degrade coatings, causing issues like fading, chalking, cracking, or other forms of deterioration over time.
During the QUV test, an abbreviation for “QUV accelerated weathering tester,” samples are exposed to UV radiation inside a machine designed to simulate the effects of sunlight. This simulation often includes moisture, either through condensation or water sprays, to replicate natural weathering conditions. The test allows for the adjustment of UV light intensity and the cycling between wet and dry conditions to mimic various climates and solar radiation levels.
These test cycles, which can last from several days to weeks, provide accelerated results. They offer predictions on how the coating will endure over months or even years in outdoor environments. After testing, the samples are evaluated for any changes in color, gloss retention, surface integrity, and other properties, in comparison to samples that were not exposed. Such testing is vital for products destined for sun-exposed settings, ensuring that the powder coating retains its aesthetic appeal and protective properties throughout its intended lifespan.
Typically, this equates to 10 – 20 years of color resistance (with a 5% fade) and about 5 years of corrosion resistance within 5 kilometers of a beach. These are estimations based on test results, but it’s important to note that our warranty does not extend to beachfront properties. For enhanced resistance in beachfront properties, we offer Qualimarin and Seaside Certified products, classified as Class 2. These are specifically designed for durability in marine or coastal environments.
Enhancement Options
Sealing Edges and Joints
Ensure that the edges, joints, and other potential entry points for moisture are properly sealed and
protected. – Use of Primers: Applying a corrosion-inhibiting primer before the topcoat can significantly reduce the risk of
filiform corrosion. Primers often contain chromates or other inhibitors that provide additional protection.
Alloy Aluminum Extrusion Certifications
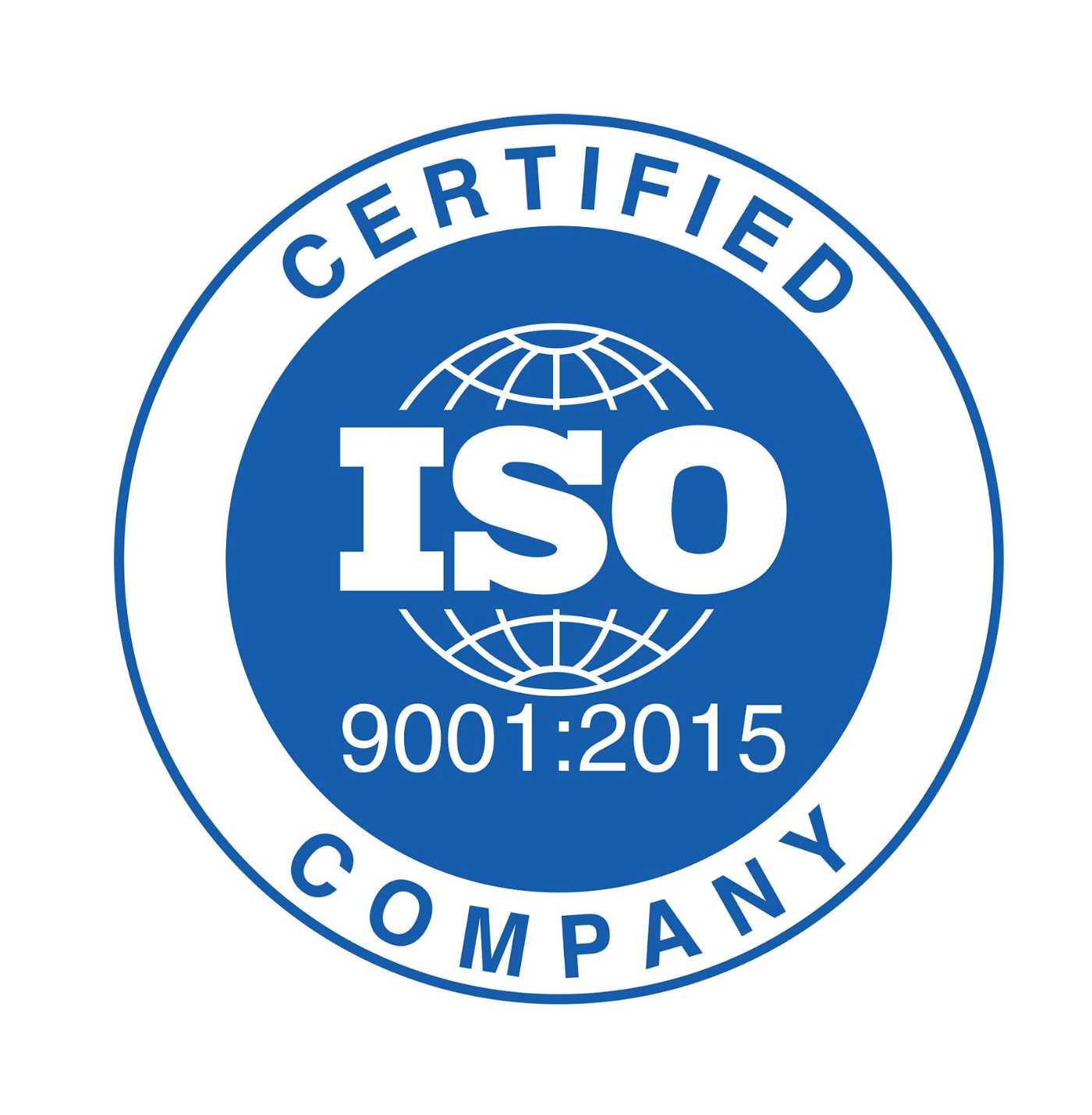
ISO 9001 2015: Quality Management System
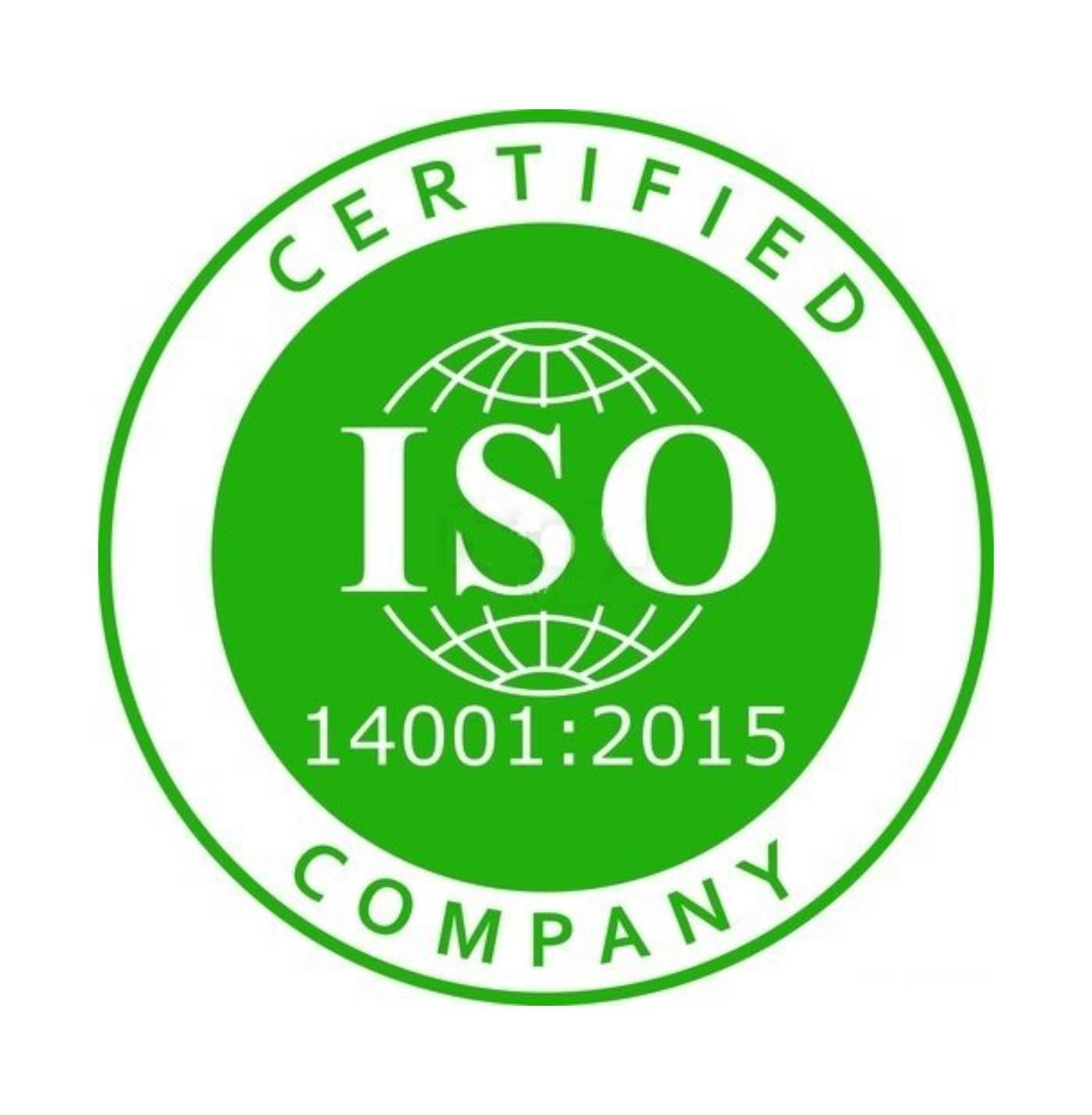
ISO 14001:2015 - Environmental Management System
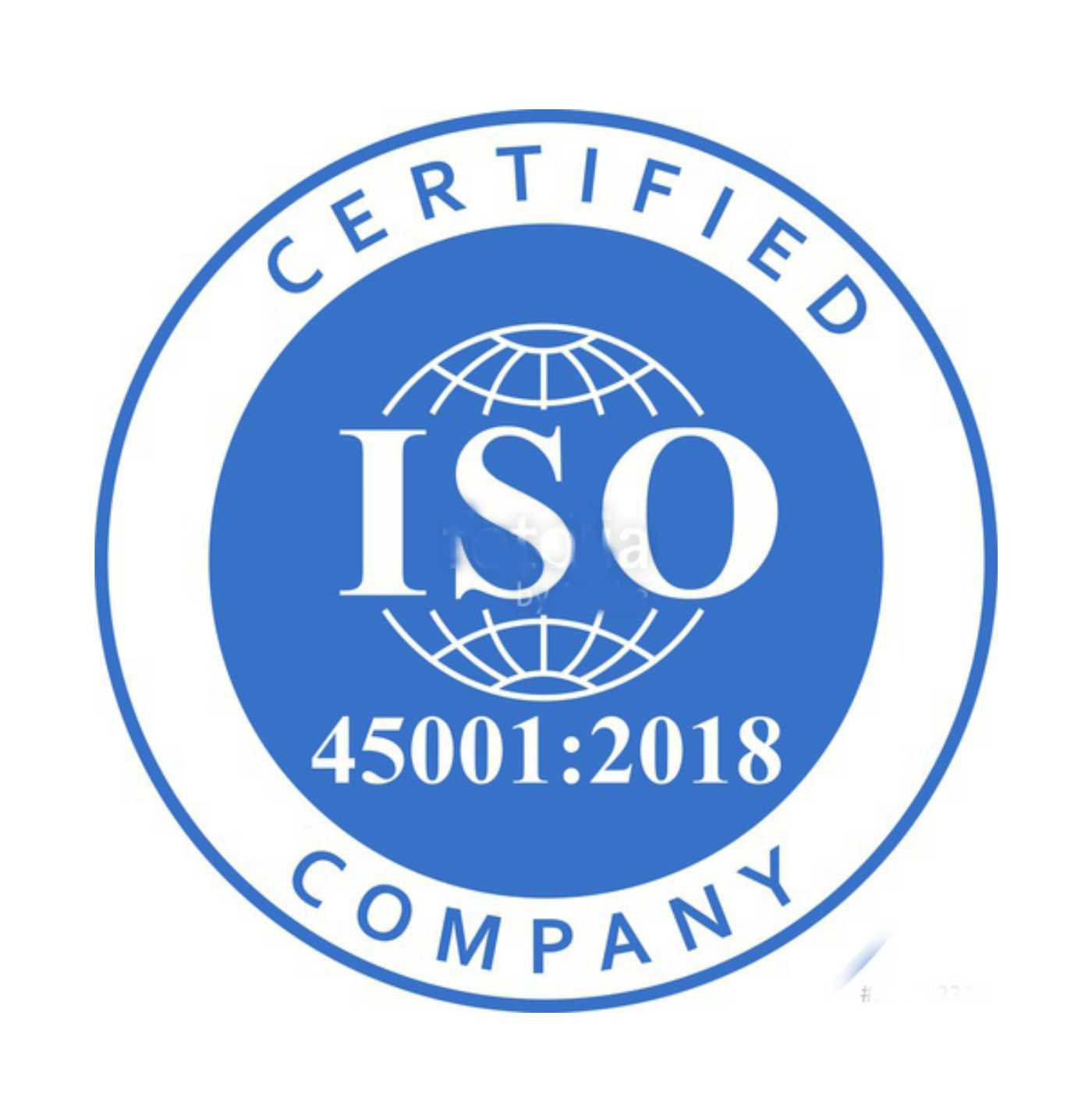
ISO 45001:2018 - Occupational Health & Safety Management System
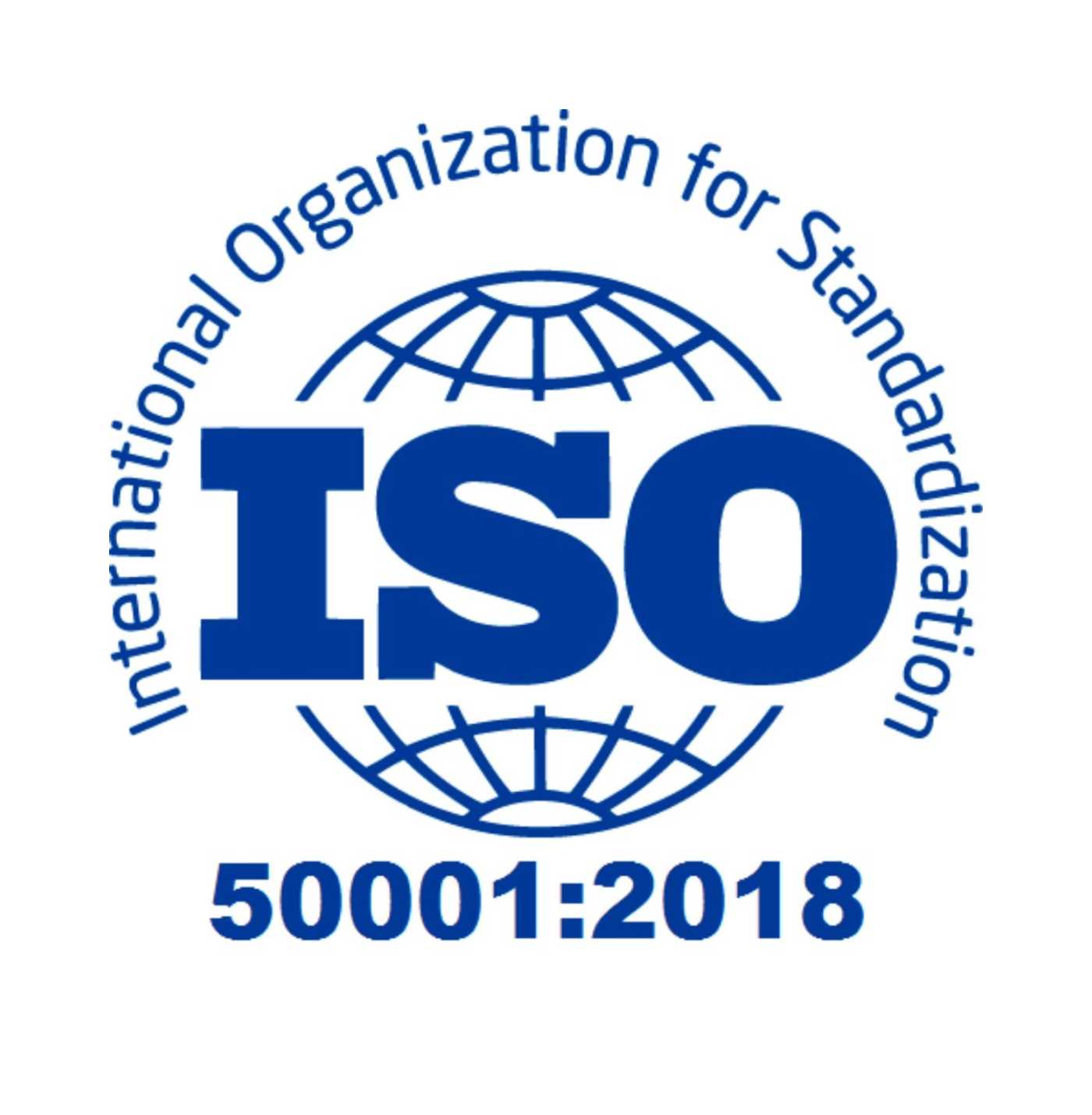
ISO 50001:2018 - Energy Management System
European Standards
Certifications and Material Excellence of Our Aluminum Products
Our products have successfully passed the rigorous TAS201, TAS202, and TAS203 testing as part of the Dade County NOA approval process and are now in the final stages of certification. We are confident in securing these credentials by the 2 nd – 3rd quarter of this year, further solidifying the trust in our products.
It is essential to highlight that our products are engineered from the finest architectural grade extruded aluminum (6063- T5 alloy), known for its exceptional durability and rigidity. This non-combustible material boasts a Class A fire rating, ensuring maximum safety. The specifics of the aluminum alloy used are: 6063 Alloy in a T5 temper, with a robust thickness of 0.047 inches (Gauge 18) and finished with an electrostatic powder coating for a durable, sublimated surface.
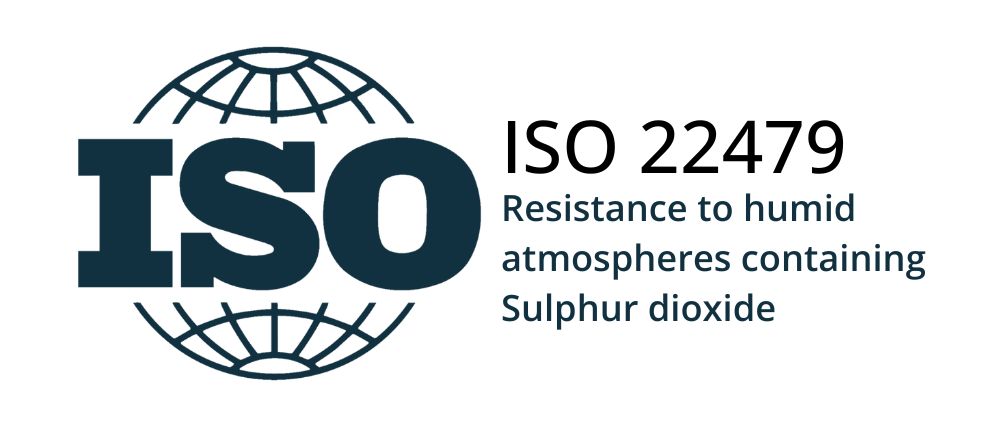
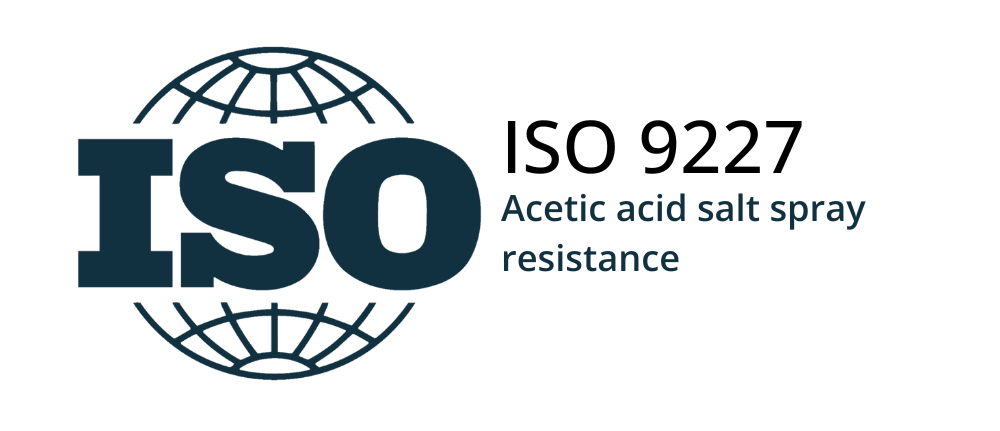
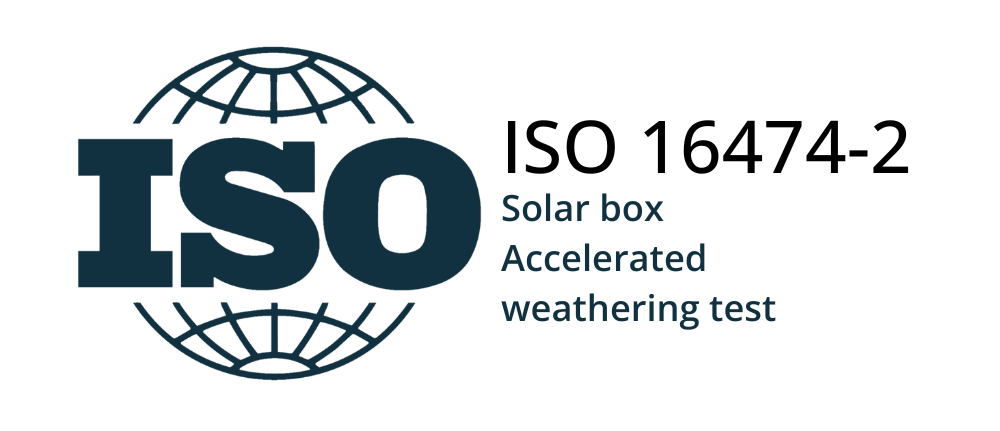
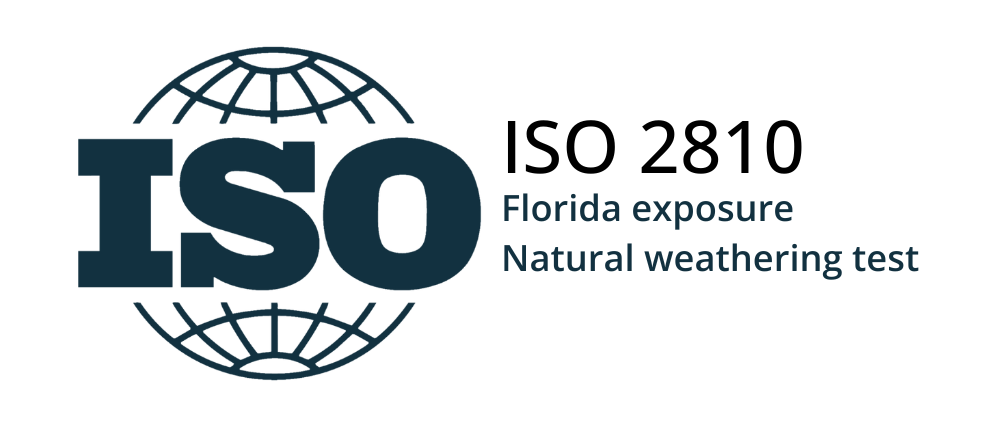
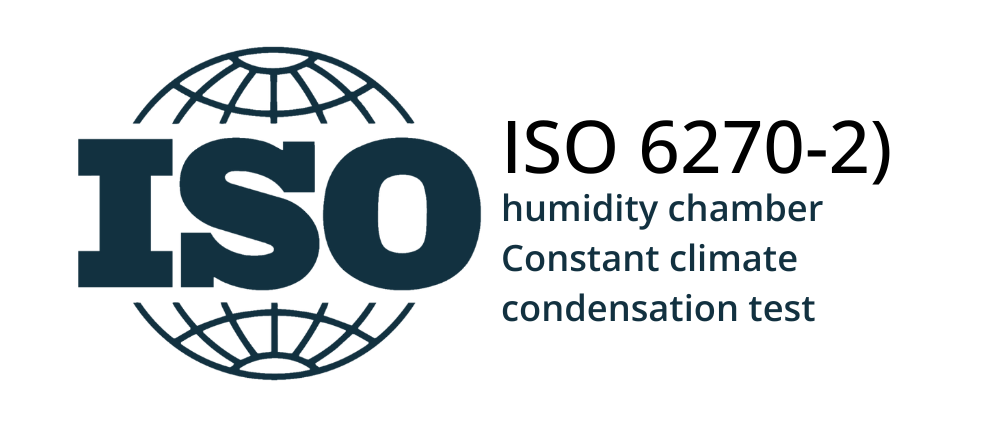
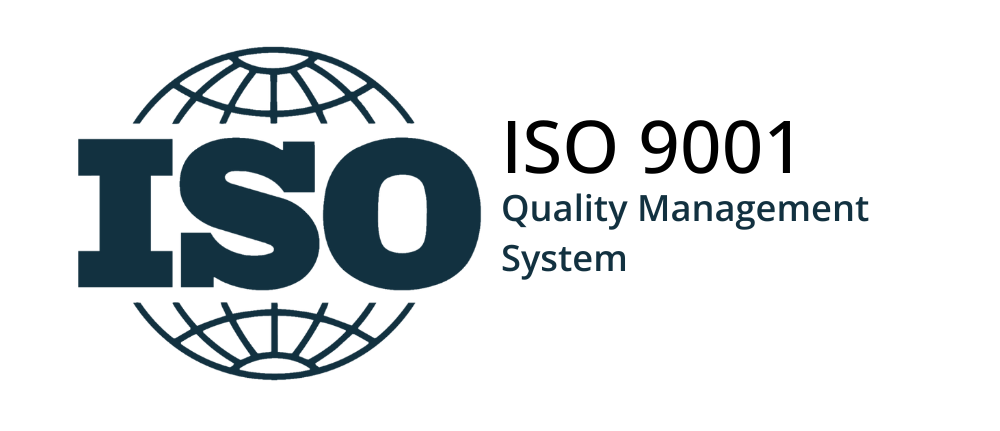
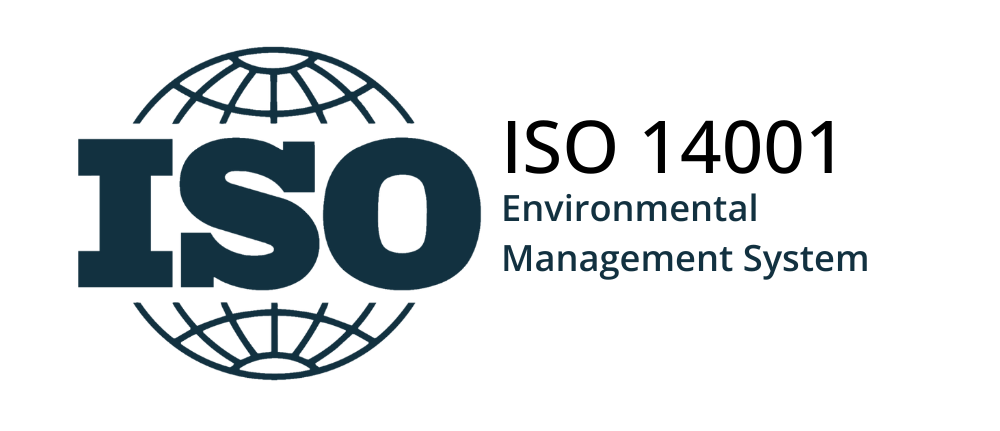
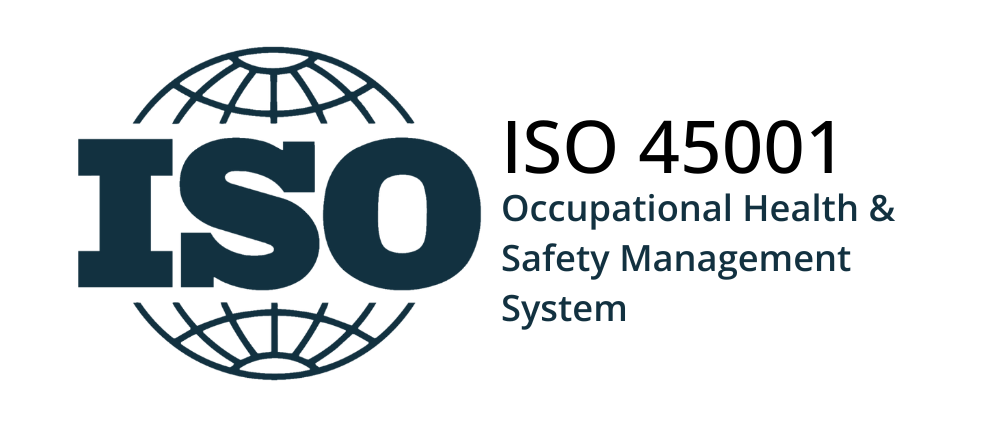
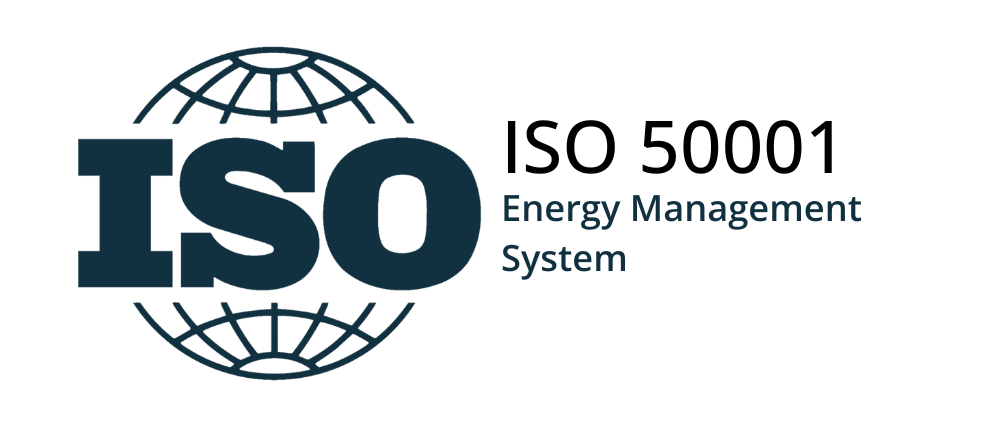
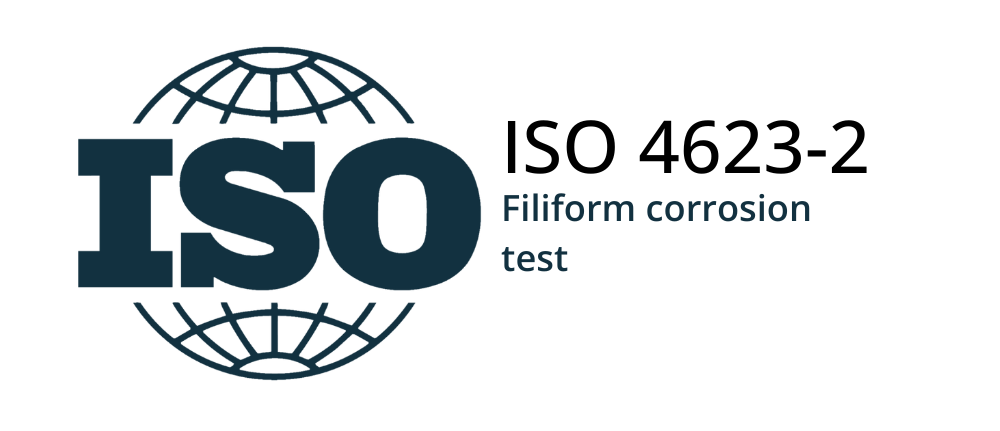
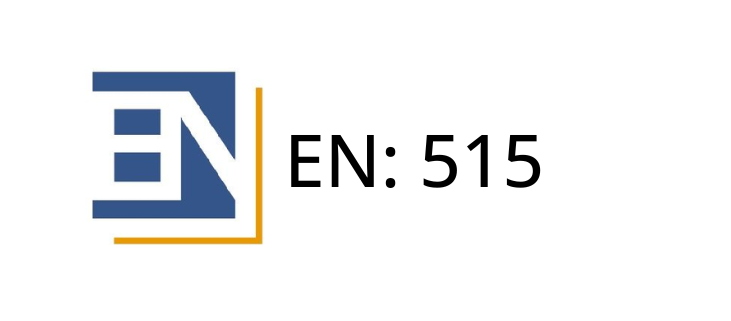
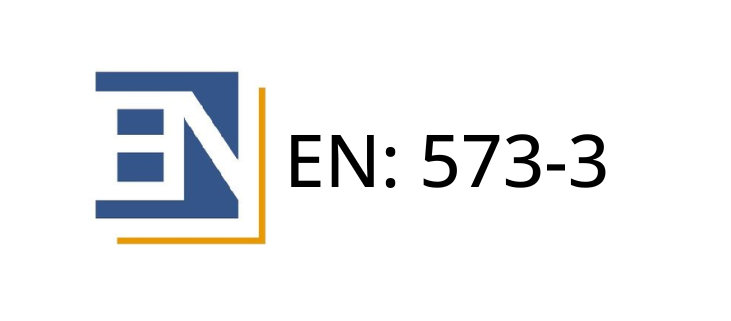
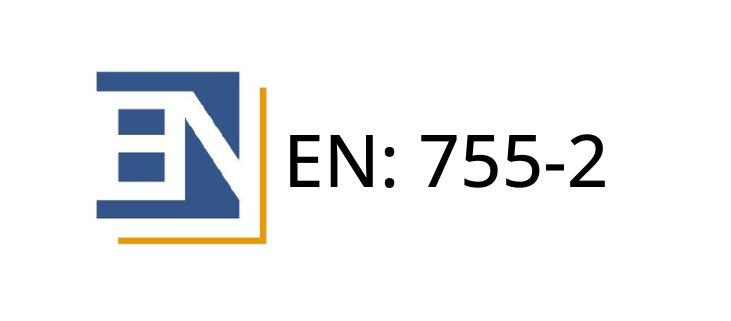
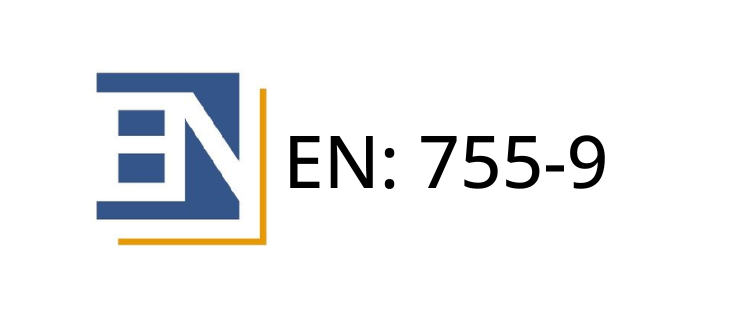
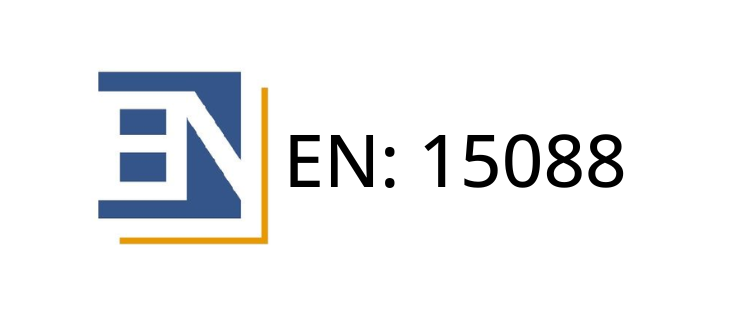
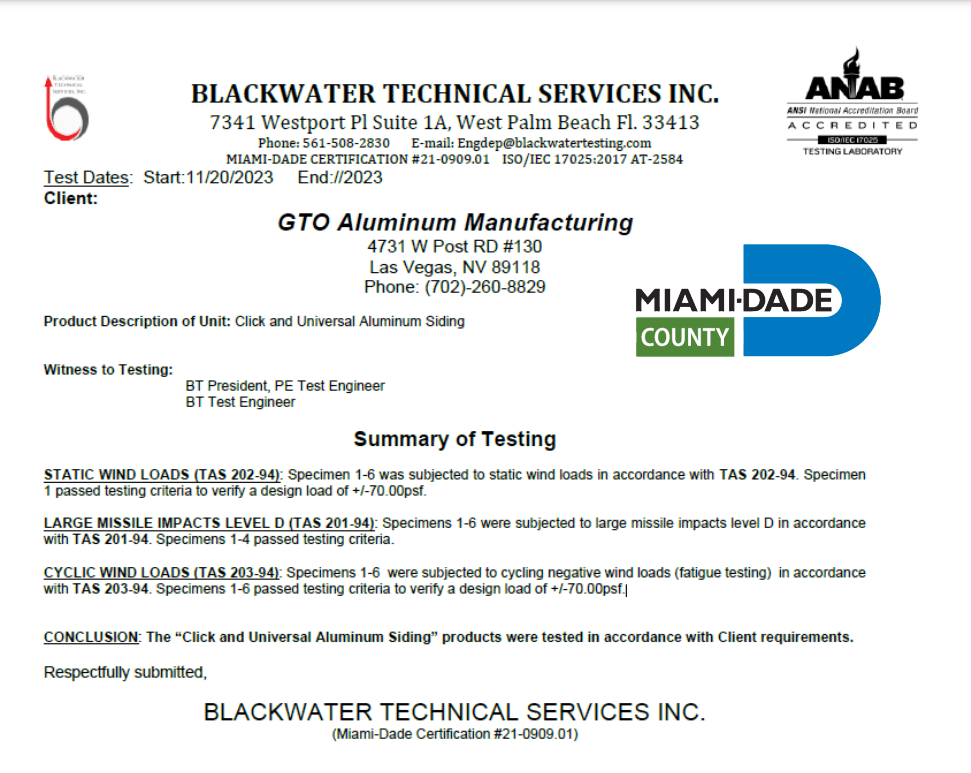
Powder Coating with Sublimation
Sublimation & Unique Custom Color Process
- The sublimation or transfer technology consists of transferring an image previously printed on a specific
film, to the aluminum profiles. - Powder paints used as sublimation bases can be formulated with polyester or polyurethane resins.
- They must have both the ability to resist the sublimation temperature (190-200 °C) and to adequately absorbs the inks transferred by the film.
The Process
Base Application
The first step in the process is the base application the profiles to give them a colored base. The purpose in this is to create the right base tone to imitate the desired type of wood or the color of the thermo - print finish that is required. Electrostatic paint is applied to the surface of the aluminum. The paints used are polyester or polyurethane resins. These finishes are highly resistant to UV rays, atmospheric agents, and corrosion.
Bagged
The ends of the profiles are protected with tape and placed in plastic film bags. These bags already have the wood pattern, or the established design printed on them using dyes.
Empty
Air is extracted from the bags through nozzles at the end of the bags, creating a vacuum. The profiles are revised so that the casing adjust to the geometry of the profile, eliminating the occluded air.
Sublimation
The profiles are introduced into an oven that is at a temperature between 190 and 220 C. Thesis where the sublimation effect on the aluminum occurs, passing the ink in the bag from a solid state to a gaseous state. After a few minutes, the coloring is transferred to the profile.
Withdrawal of the film
Air is introduced to the profiles in the bags do that the film can be removed, cooling them at the same time.
Powder Coating Certifications
USA
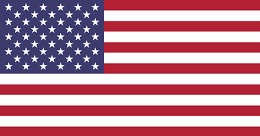
Q-SUN XE-3 HS – passed the Accelerated weathering test by SUBLITEX.
European Standards / EU standards
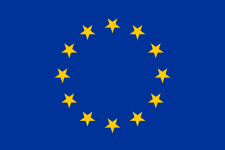
EN 515, EN 573-3, EN 755-2, EN 755-9, EN 12020-2
QUALICOAT
- Quality Mark of Electrostatic Coating of Aluminum Surface according to the QUALICOAT Specification
- Quality Label for Powder Coated Aluminum Surfaces according to QUALICOAT Specification
- Decoration Quality Mark (Sub-color) Electrostatically Painted Aluminum Surface according to QUALIDECO specification
- Quality Label for Decoration (Sublimation) of Powder Coated Aluminum Surfaces according to QUALIDECO Specification QUALIMARINE
- Quality Mark for Electrostatic Painting of Aluminum Surface according to the French QUALIMARINE specification
- Quality Label for Powder Coated Aluminum Surfaces according to the French QUALIMARINE Specifications QUALANOD
- Quality Label for Anodized Aluminum Surface actor to to QUALANOD Specification
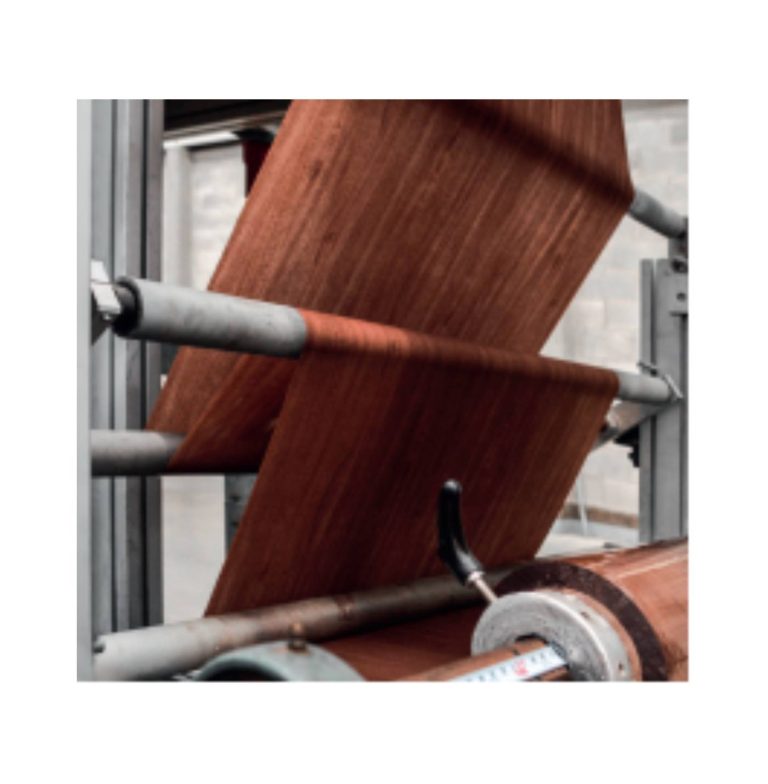
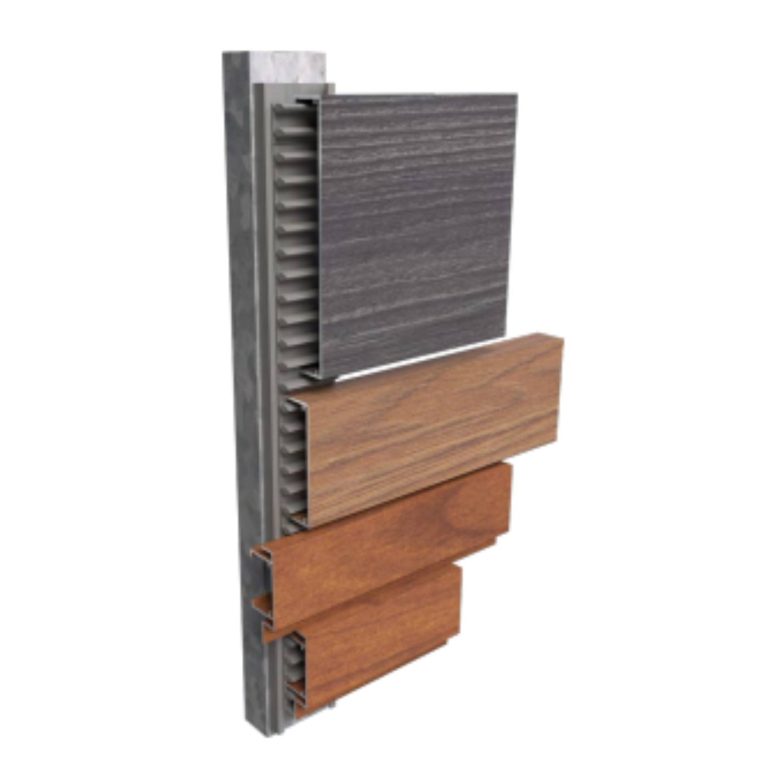
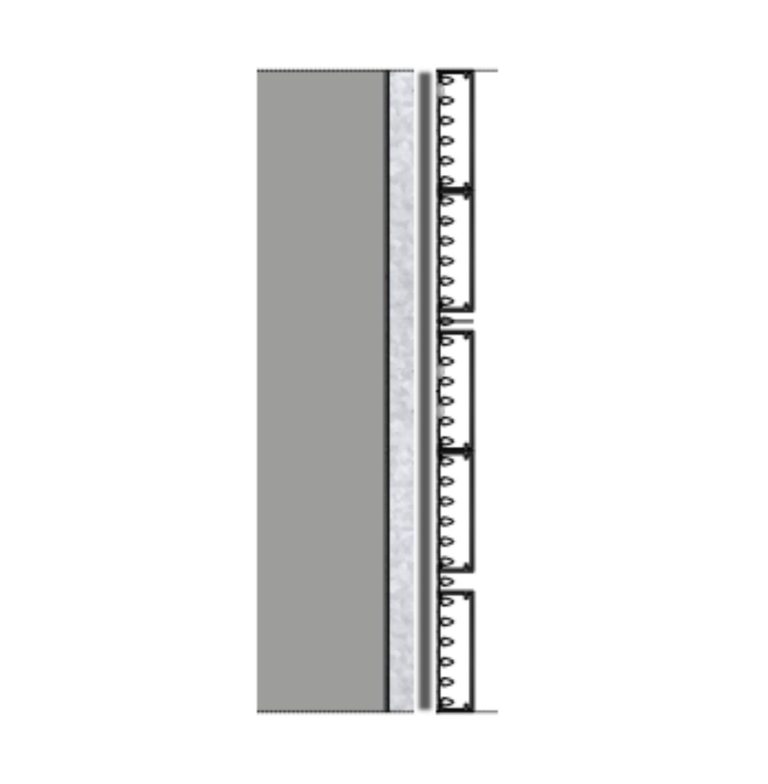
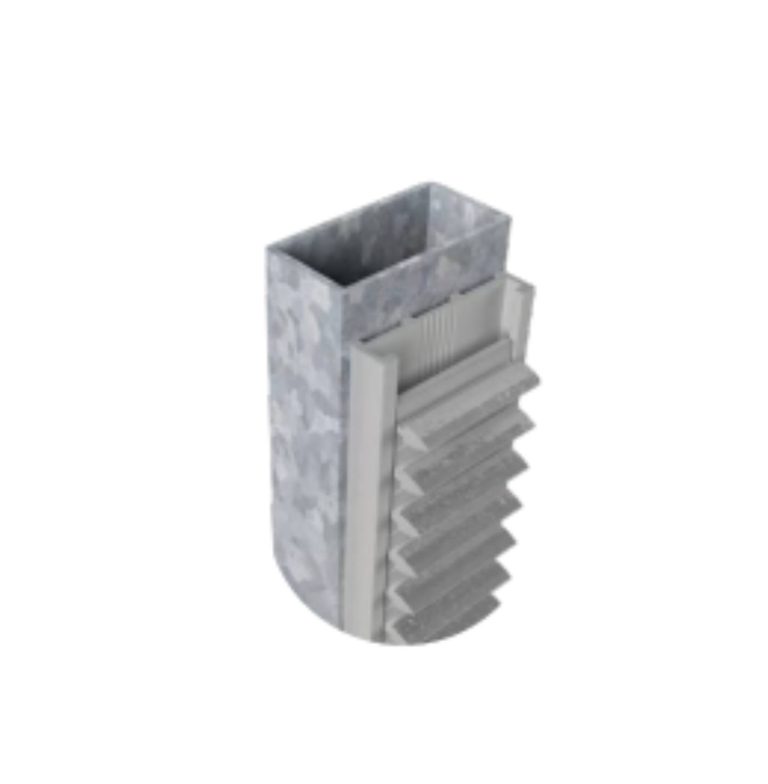
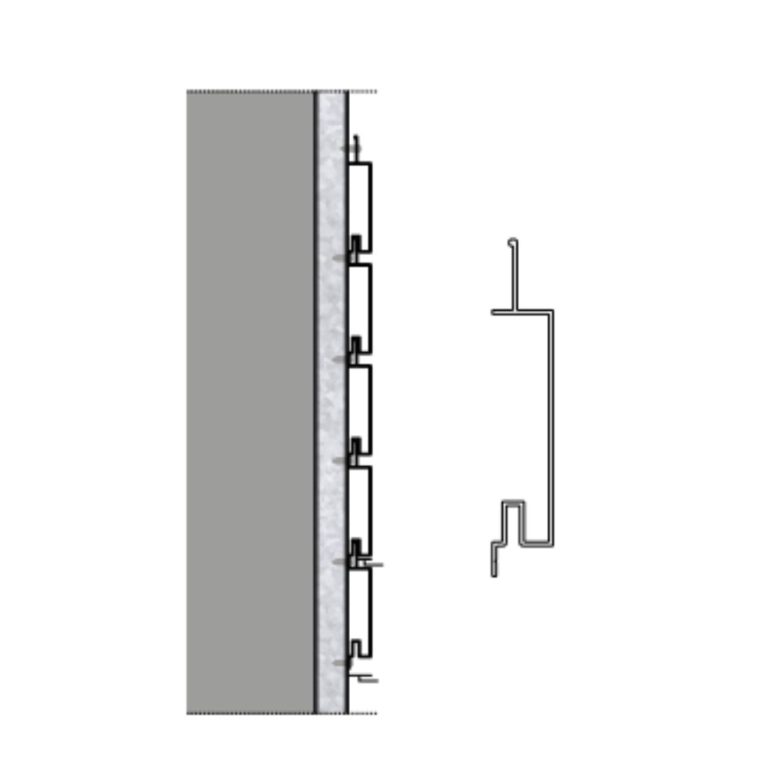

FAST
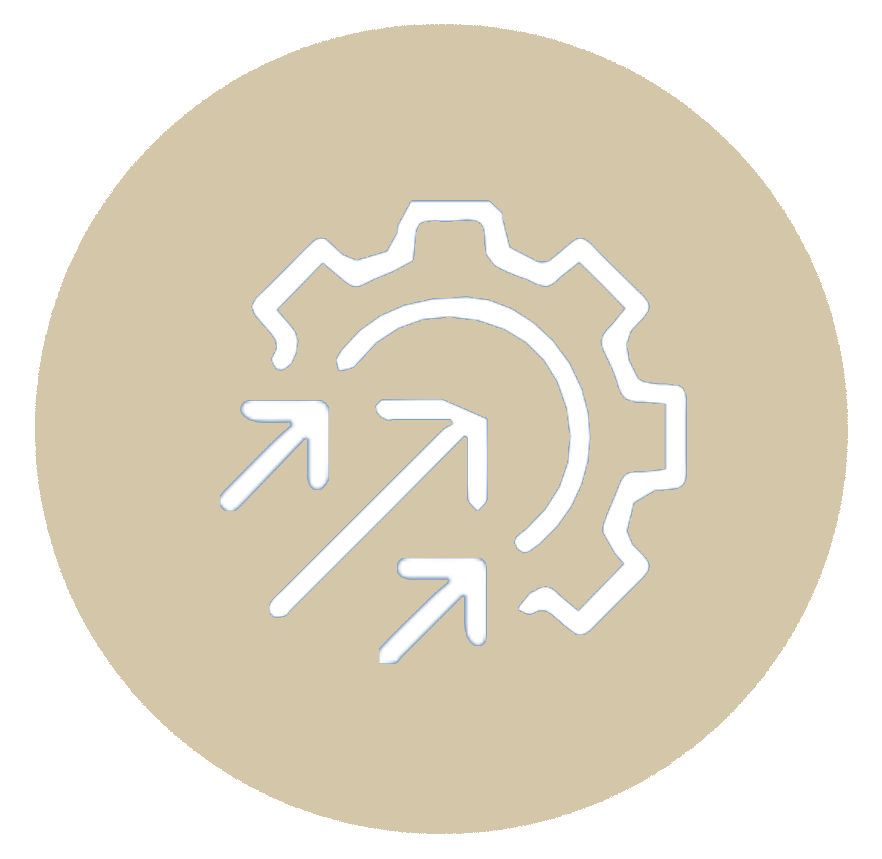
EFFICIENT
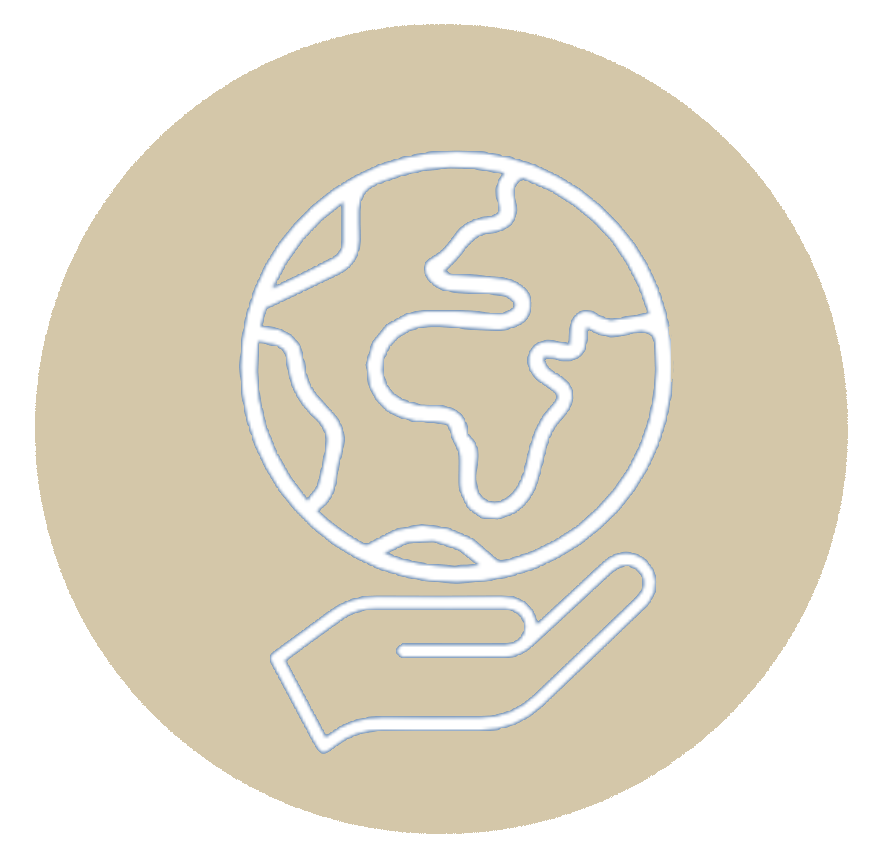
SUSTAINABLE

STRONG
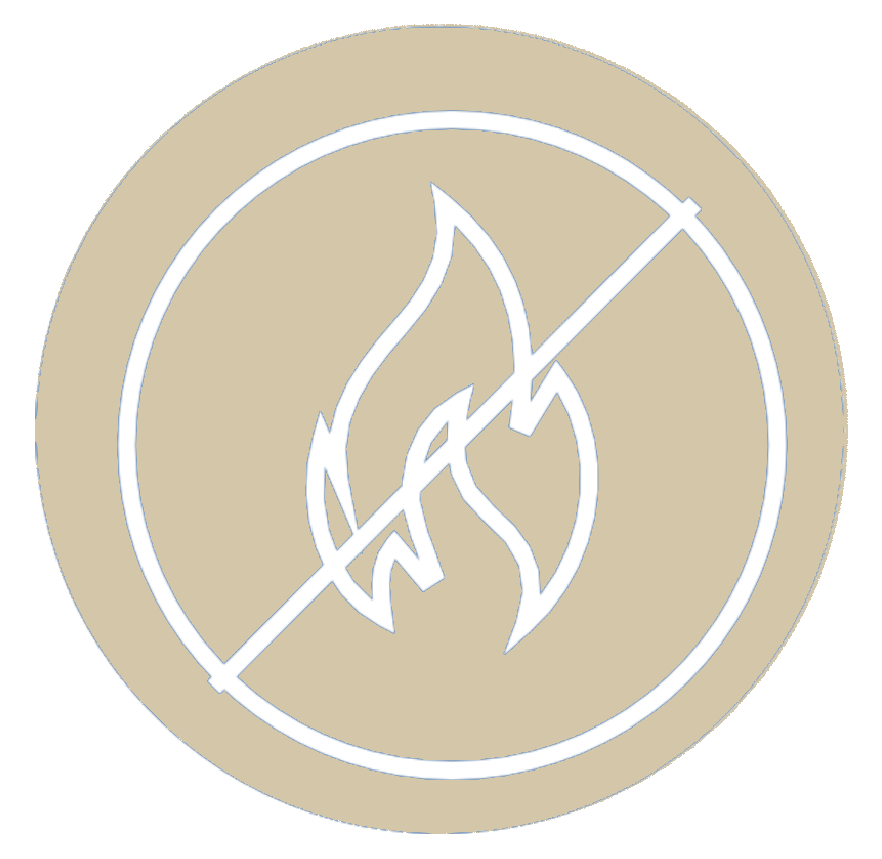
INCOMBUSTIBLE
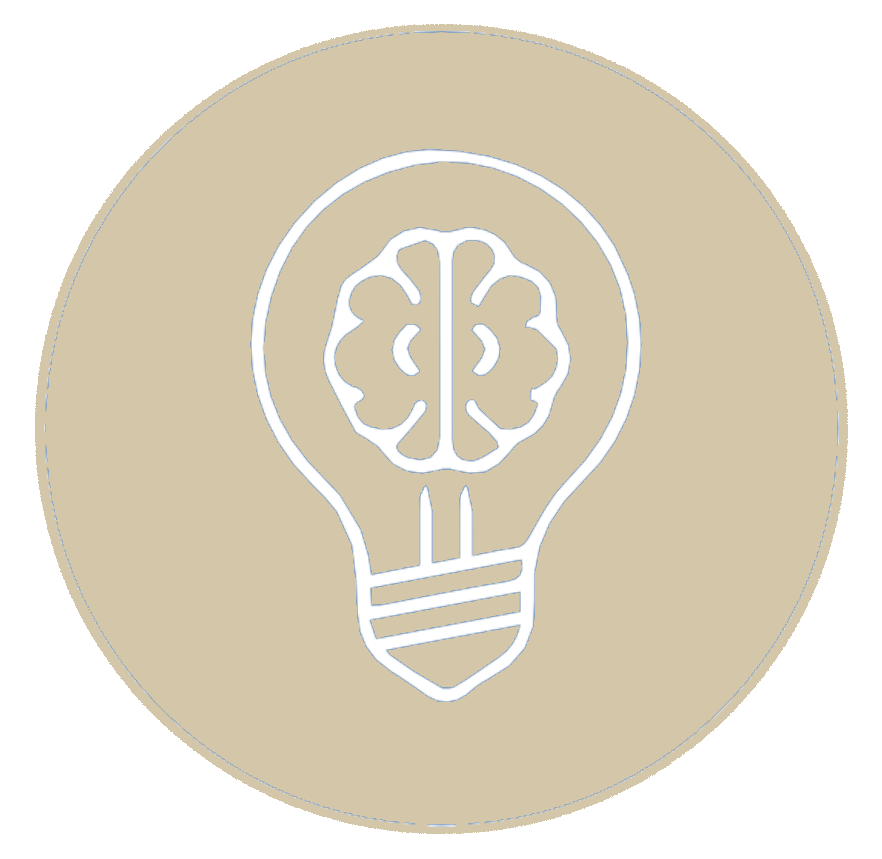
SMART
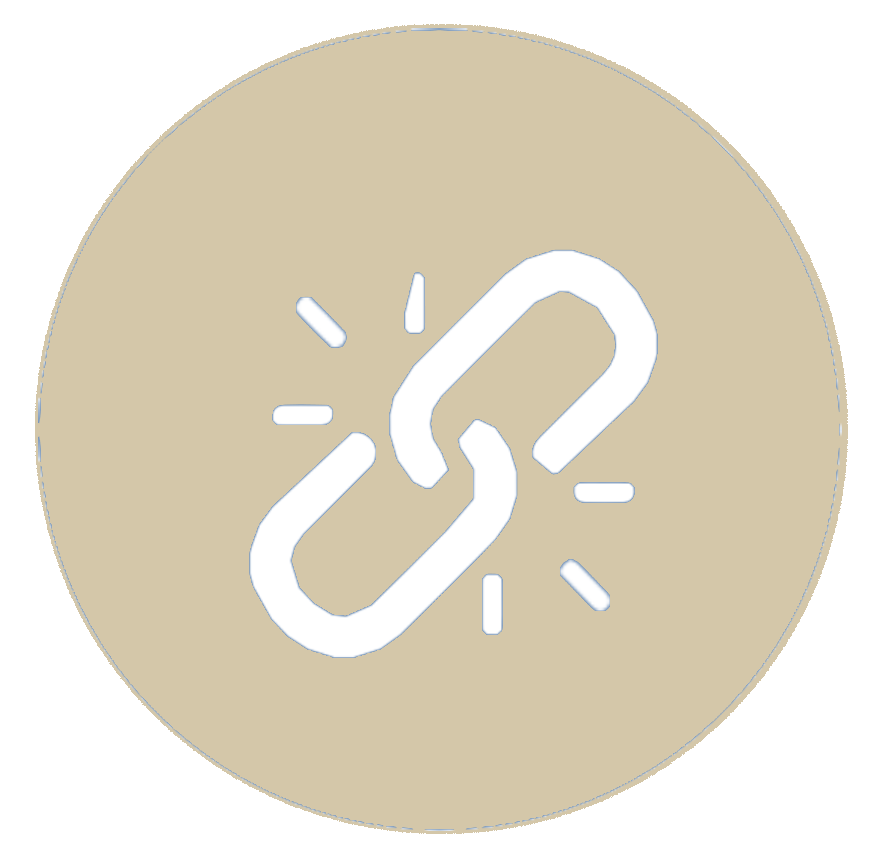
DURABLE

SAFE
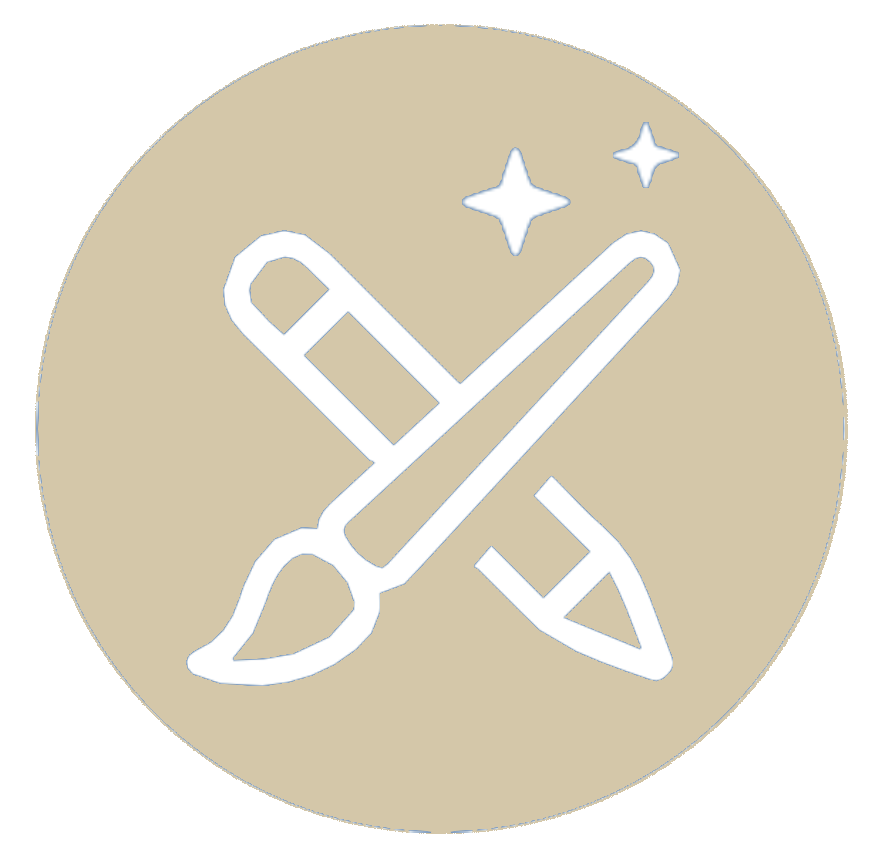
MODERN DESIGNS
Feature Rating Comparison
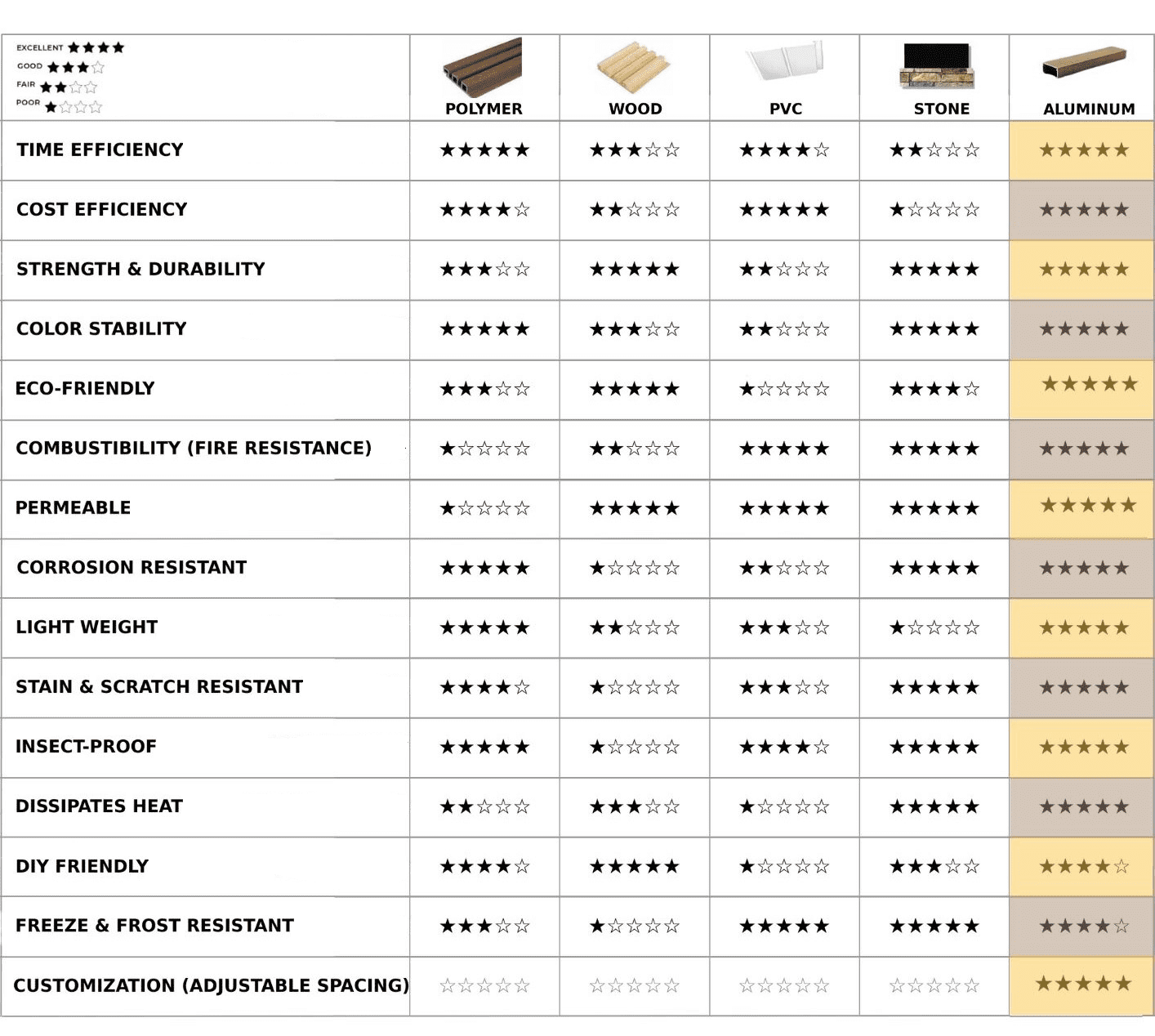