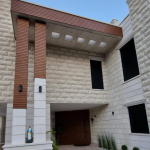
Aluminum Cladding in Public Buildings: How to Balance Aesthetics and Functionality
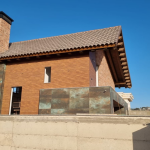
Future Trends in Aluminum Cladding Textures and Patterns

Ever wondered how the right aluminum coating can drastically enhance the performance and longevity of your products?
Aluminum, known for its durability, lightweight nature, and corrosion resistance, is a popular choice for various applications.
Enhancing these inherent properties through various coatings can significantly extend the life and improve the performance of aluminum products.
This guide delves into the different types of aluminum coatings, offering insights into how each type serves its purpose.
Introduction to Aluminum Coating
Aluminum coatings are more than just a layer of protection; they are a critical enhancement to aluminum’s natural properties.
These coatings can provide additional corrosion resistance, improve aesthetic appeal, and even add functionality.
The process of choosing the right aluminum coating depends on the intended application, environment, and specific requirements of the product.
Understanding the variety of aluminum coatings available is the first step in appreciating their versatility and efficiency.
Whether you’re in construction, automotive, aerospace, or culinary industries, there’s an aluminum coating suitable for your needs.
Anodizing: Durable and Decorative
Anodizing is one of the most common and versatile aluminum coatings, known for its ability to enhance corrosion resistance.
This electrochemical process thickens the natural oxide layer on the surface of aluminum parts, making them more durable.
Anodized aluminum can also be dyed in various colors, providing aesthetic flexibility alongside functional benefits.
The process involves submerging aluminum in an acid electrolyte bath and passing an electric current through the medium.
This results in the aluminum surface being converted into aluminum oxide, which is hard, durable, and resistant to corrosion.
Anodizing is ideal for architectural components, consumer electronics, and kitchen appliances where both appearance and durability are important.
Powder Coating: Vibrant and Versatile Aluminum Coating
Powder coating is a dry finishing process that applies a protective and decorative finish to aluminum.
The powder used in the process is a mixture of finely ground particles of pigment and resin, which is electrostatically sprayed onto the surface to be coated.
The coated item is then cured under heat to form a skin-like layer that is tougher than conventional paint.
This type of coating is known for its extensive color options, superior finish, and environmental friendliness, as it emits zero or near-zero volatile organic compounds (VOCs).
Powder coating is widely used in automotive parts, bicycles, home appliances, and garden furniture for its ability to withstand harsh conditions.
Chromate Conversion Coating: Corrosion Resistance Aluminum Coating
Chromate conversion coating is a type of aluminum coating that enhances corrosion resistance and prepares the surface.
This chemical process creates a thin protective layer on the surface, which can improve adhesion for additional coatings and provide electrical conductivity where needed.
Commonly referred to by trade names like Alodine or Iridite, chromate conversion coatings are used in aerospace and military.
The process is valued for its quick turnaround and ability to offer significant protection without altering the part’s dimensions.
E-Coating: Precision and Uniformity
Electrophoretic deposition, or e-coating, is a method that uses electrical current to deposit paint or resin on a conductive part.
This process ensures that even the most complex surfaces are coated uniformly, providing excellent adhesion and corrosion resistance.
E-coated aluminum parts have a smooth, uniform finish that is ideal for automotive parts, hardware, and any application requiring precise and consistent coverage.
E-coating is particularly beneficial for parts with intricate shapes, ensuring that every nook and cranny is covered.
This results in a lightweight, durable finish that can significantly extend the lifespan of aluminum components.
Thermal Spraying: High Performance Under Extreme Conditions
Thermal spraying involves melting a coating material and spraying it onto the aluminum surface, where it solidifies to form a protective layer.
This process can use metals, alloys, ceramics, or plastics as coating materials, offering a wide range of properties.
Thermal spraying is used in aerospace, automotive, and energy sectors where components are exposed to extreme conditions.
It’s particularly beneficial for restoring the dimensions of worn parts or providing specialized functionality, like heat resistance or electrical conductivity.
PVD Coating: Futuristic Finish
Physical Vapor Deposition (PVD) is a vacuum coating process that produces a brilliant decorative and functional finish.
PVD coatings are made of metals such as titanium, zirconium, and aluminum nitride, which offer exceptional hardness and resistance.
This type of coating is commonly used in decorative hardware, plumbing fixtures, and automotive trim for its ability to maintain appearance.
The PVD process involves vaporizing a solid metal into a plasma of atoms or molecules, which are then deposited on the electrically conductive aluminum.
The result is a thin, uniform, and durable coating that can significantly enhance the aesthetic appeal and longevity of aluminum.
PVD coatings are also environmentally friendly, emitting no harmful chemicals during application.
Silicon Coating: Heat Resistance and Electrical Insulation
Silicon coatings on aluminum are prized for their exceptional heat resistance and electrical insulation properties.
This type of coating is typically applied through a spraying process, where a silicon-based compound is layered onto the aluminum surface.
The result is a coating that can withstand high temperatures without degrading, making it ideal for use in engines, exhaust systems, and electrical components.
Beyond its heat resistance, silicon coating also provides excellent electrical insulation, which is crucial for electronic and electrical applications.
By preventing electrical currents from passing through the aluminum surface, silicon coatings ensure safety and reliability.
Fluoropolymer Coatings: Non-stick and Chemical Resistant
Fluoropolymer coatings, such as Teflon, are well-known for their non-stick properties, but they also offer excellent chemical resistance and durability.
These coatings are applied to aluminum to create surfaces that resist adhesion and are easy to clean.
It is particularly useful in cookware, bakeware, and processing equipment where sticky or corrosive substances are involved.
In addition to their non-stick qualities, fluoropolymer coatings are resistant to a wide range of chemicals, making them suitable for use in harsh environments.
Their ability to maintain integrity at high temperatures further extends their application range to areas where heat resistance is crucial.
Marine Coatings: Protection Against the Elements
Marine coatings are specially formulated to protect aluminum in marine environments, where salt water and harsh weather can cause significant corrosion.
These coatings provide a barrier that prevents moisture and salt from coming into contact with the aluminum.
Marine coatings are designed to withstand the rigors of the marine environment, including UV exposure, salt spray, and fluctuating temperatures.
They are essential for maintaining the integrity and appearance of boats, docks, and offshore structures.
Conclusion: The Right Aluminum Coating for Every Need
As we’ve explored, aluminum coatings offer a diverse palette of solutions, each tailored to amplify aluminum’s inherent properties.
These coatings transform aluminum into an even more versatile material, capable of facing enhanced aesthetic demands, combating corrosion, enduring high temperatures, and providing unique functionalities like non-stick surfaces.
Understanding the wide array of available coatings empowers manufacturers and consumers to make well-informed choices.
Ensuring aluminum products not only meet but exceed performance expectations in their specific applications.
As we look forward to the innovations that lie ahead, the role of aluminum coatings in technological advancement becomes increasingly significant.
Ongoing research and development promise new, groundbreaking applications and improvements in material science.
Here’s where GTO Aluminum steps into the picture. GTO Aluminum is at the forefront of leveraging these innovative coating technologies to enhance the performance and longevity of aluminum products.
With a commitment to quality and innovation, GTO Aluminum provides expert guidance and access to a wide range of coating options tailored to meet specific needs.
Whether it’s for aerospace, automotive, marine, or culinary applications, GTO Aluminum can help identify the optimal coating solution that aligns with specific requirements, environmental conditions, and performance criteria.